Improvements to ASC casting materials
2025-07-14
The molten iron produced by the blast furnace flows through the iron trough to the molten iron ladle or torpedo car, and then is transported to the steelmaking plant. The molten iron is immersed in the iron trough for a long time, so the refractory materials inside the iron trough require extremely high performance. ASC castable is the main material used in the blast furnace iron trough. It must resist the strong impact force generated during the tapping of the blast furnace and the physical and chemical erosion of molten iron and slag.
The raw material management system for -SiC-C castable has been established, and its construction method is increasingly tending towards self-flowing. This change in method is mainly due to improvements in equipment PSD and the use of highly efficient K-reducing agents. The development trend of the fusion system for ASC refractory castable is towards the development of SiO2-free and CaO-free materials. At present, AI203-SiC-C castable without any cement binder has been developed and is being gradually promoted. For the damage mechanism of ASC refractory castable during use, corresponding measures have been taken to improve or enhance it to a certain extent. Regarding the corrosion of slag/iron on AI203-SiC-C castable, it is more important to consider it from the perspective of modifying the raw material material. Some raw materials that can change the properties of the slag or itself are added to the system to reduce the corrosion level of the raw materials and extend the service life. For example, by adding MgO or MA, the dissolution rate of its own components into the slag and the products of the reaction time between the slag and the AI203-SiC-C castable are changed, thereby changing the thermal expansion of the raw materials. Low-melting-point substances are also added to form a highly efficient liquid phase under lower conditions to block pores and improve the permeability balance of the raw materials. To improve the oxidation resistance of the iron trough castable, Henan Zhonggong New Materials Co., Ltd. adds the antioxidant CaB6-SiC powder to improve the oxidation resistance and other properties of the ASC castable.
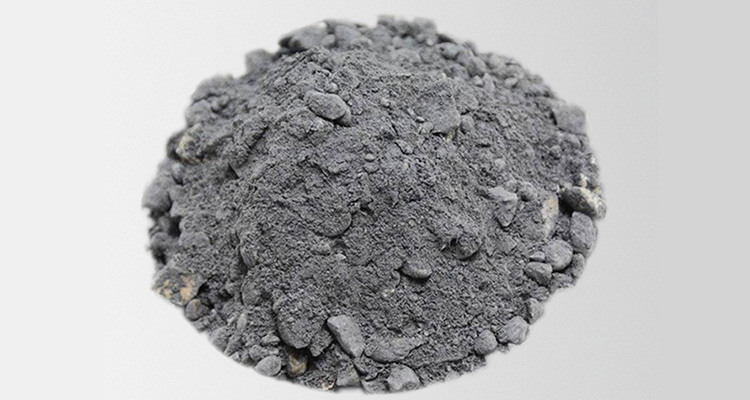
The appropriate introduction of the antioxidant CaB6-SiC can improve the density and strength of the ASC castable. It can also reduce the thickness of the decarburization layer on the sample cross-section, which has a positive effect on improving the oxidation resistance of the material. In a comprehensive comparison, when the amount of antioxidant CaB6-SiC introduced reaches 1%, the iron trough castable has the best performance indicators, and the on-site application has achieved good results.
Based on experimental data, the castable with 1% antioxidant CaB6-SiC added was applied in actual on-site applications. Two tapping fields of the blast furnace were used, each with a main trough length of 18m and a slag trough length of 12 branches and 42m; a total of 90t of materials were used, including 55t for the main trough and 71t for the slag trough. The service life was 83 days, the tapping volume was 182,000t, and the best iron tapping record was created.
Previous Page:
Real-time Information
■
—
2025-07-25