Energy conservation and emission reduction----Lightweight thermal insulation brick
2025-07-11
Kiln lining insulation is one of the most effective ways to reduce heat loss and thermal radiation from kilns. Currently, lightweight, heat-insulating, high-temperature materials are often used in the insulation linings of high-temperature equipment such as decomposition furnaces, rotary kilns, and high-temperature kilns. These materials effectively isolate the heat transfer between the inner and outer enclosure structures, reducing thermal radiation from high-temperature equipment. Lightweight, heat-insulating, high-temperature materials are porous materials with low bulk density, high porosity, good thermal insulation performance, and high-temperature resistance. On the one hand, to reduce the thermal radiation of high-temperature equipment, lightweight, heat-insulating, high-temperature materials should have excellent high-temperature insulation performance, i.e., they should have an extremely low thermal conductivity. Generally, the thermal conductivity of lightweight, heat-insulating, high-temperature materials is required to be less than 1.0W/(m·K) (200℃), but with the increase in the operating temperature of high-temperature equipment, higher requirements are placed on the thermal conductivity of the materials to meet the safety requirements of high-temperature industrial production. On the other hand, lightweight, heat-insulating, high-temperature materials should have sufficient strength to ensure the service life of the insulation layer and prevent the collapse of the furnace chamber, which could damage the sintered materials inside the furnace, causing economic losses and, more seriously, safety accidents.
In response to the above situation, Henan Zhonggong Refractory New Materials Co., Ltd. has developed Using nano-silicon sol as a binder and employing an absorption filtration molding method to produce high-strength nano-insulating lightweight bricks (as shown in Figure 1) These bricks can be directly used in the working parts of high-temperature kilns, reducing the amount of materials used in the kilns and improving their thermal efficiency. They can replace the currently widely used alumina hollow ball bricks. This material has a lower bulk density and higher strength than alumina hollow ball bricks and can be used in high-temperature environments of 1400-1500℃, which is higher than other nano-lightweight insulation materials on the market. The main performance indicators of nano-insulating lightweight bricks and hollow ball bricks are shown in Table 1.
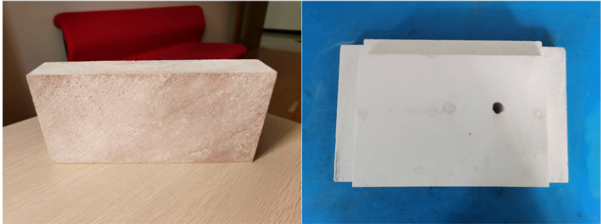
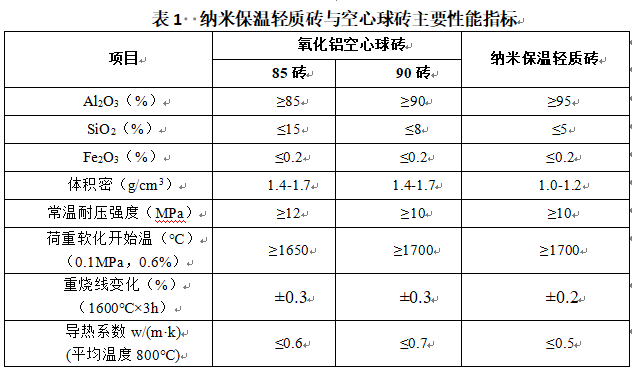
After 3 months of use, the hollow ball bricks in the high-temperature heating furnace lining constructed using nano-insulating lightweight bricks and traditional hollow ball bricks cracked and were severely damaged, while the new nano-insulating lightweight bricks developed by Henan Zhonggong Refractory New Materials Co., Ltd. remained in good condition without cracking or damage (as shown in Figure 2).
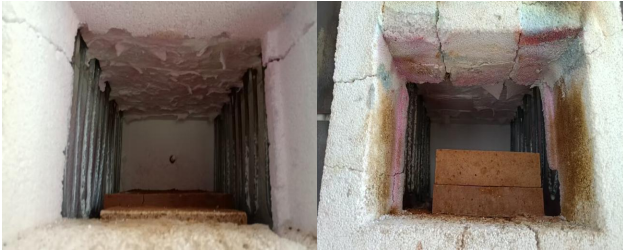
Figure 2: Condition of nano-lightweight bricks and traditional hollow ball bricks before and after use
Energy conservation and emission reduction, and green development are inevitable requirements for the development of human society. High-temperature kilns are important equipment in industrial production. The new type of nano-aluminum oxide composite lightweight insulation material can be used in kilns in the metallurgical, refractory materials production, ceramic, and chemical industries. It not only replaces traditional alumina hollow ball bricks and lightweight mullite bricks, but can also partially replace corundum bricks and corundum mullite bricks to achieve energy conservation and emission reduction.
Previous Page:
Real-time Information
■
—
2025-07-25